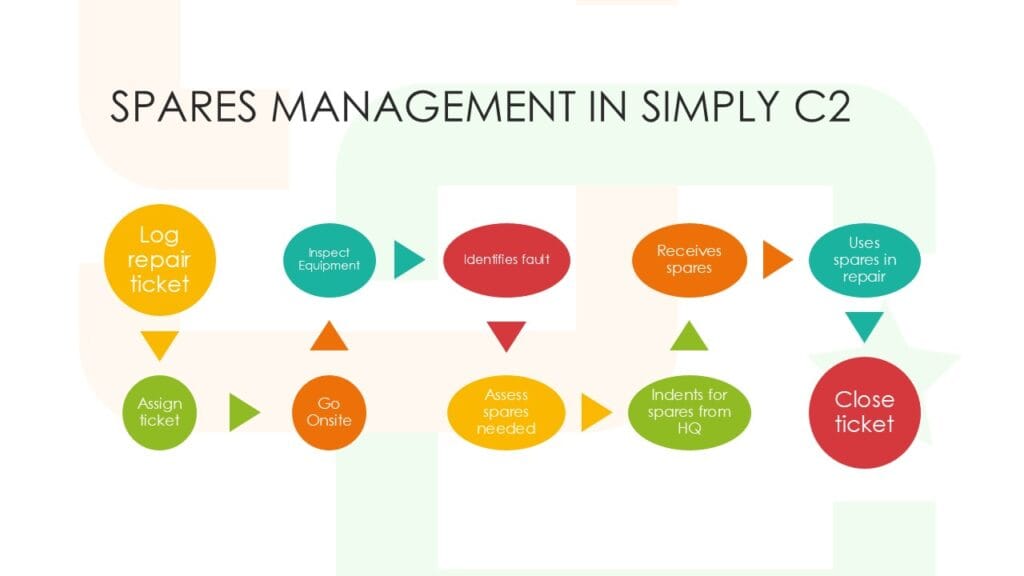
Spare Parts Management is Essential for Inventory Control in Maintenance Operations
Simply C2 offers the most comprehensive implementation of service spares management in a service CRM. There are two main costs in a customer service operation: spare parts usage and time spent (labour). Spare parts tend to be expensive, making it crucial to track them effectively.
There are two primary challenges in spare parts management:
- Inventory holding costs: You don’t want to stock inventory for extended periods; working capital is expensive, and you should only stock fast-moving spare parts.
- Unavailability/Stock-out: Not having the right part available can necessitate another site visit with the spare part. This can lead to delays and decreased customer satisfaction.
In spare parts management, it’s about striking a balance between these two key objectives. Additionally, the system must guide maintenance technicians about the parts to be used during maintenance operations.
So, the spare parts management module of any Customer service CRM has to ideally
- Be configurable: allow the user to edit, update and delete parts from the system. Also, be able to map the parts to equipment models so that the technician does not use an incompatible part with an equipment.
- Have a spare parts (along with labour) repair estimate configurator which can be used easily to generate an itemized repair quote.
In this post, I’ll explain the standard workflows in the system. This will help you understand the system’s versatility and its current limitations. Please leave your comments below if you see any improvement opportunities. Remember, you can always register for a free trial to explore not just the spare parts management module but the entire service CRM.
The Role of Part Numbers in Service Parts Management
Spare parts management is crucial in any service organization. All equipment may require spare parts during maintenance operations. All spare items have a part number and a description. The same part might be used to repair different equipment, so you can optionally map a single part to one or many pieces of equipment. Naturally, a single piece of equipment may require multiple spare parts.
Parts may or may not have a serial number. Typically, high-value components or modules used as spares have serial numbers. Simply C2 handles both scenarios equally well, whether parts have serial numbers or not. It’s admin-configurable, allowing you to define a category of parts as needing serial numbers, and Simply C2 will manage it accordingly.
Who does this tagging help? Obviously, it makes the job of the maintenance technicians much easier during preventive maintenance and corrective maintenance tasks.
The Operational Roles in Parts Management
All frontline executives and managers play important roles in spare parts management for maintenance. They can indent for spares and use them to resolve service tickets. Besides them, two roles in the system can “load the system” with spare stock:
- Admin
- Spare Parts Manager (Spares warehouse in-charge)
The Admin or Spare Parts Manager also needs to create spare models and link them to one or more equipment models. Any “line executive or manager” in a service role (technician, service exec, or service manager) can indent for spares. Any supervisor can approve parts and ship them. Approvals and shipments can be partial or full. All shipments are made directly to the indenter.
Activities Related to Spares: Stocking, Indenting, and Shipping
For maintenance technicians to have spare parts available, they need to indent for them. The entire indent and approval flow is tracked. There are two types of indents: those specifically for closing a ticket and those for stocking. Any line executive or manager in the service role can indent for spares, and any of their direct managers can approve.
The system treats ticket-related indents as urgent and auto-escalates them all the way up if needed to the person who has stock.
- Every ticket requires at least one level of approval; so at least your immediate manager must approve.
- If your manager doesn’t approve, it might be because they don’t have stock; they can “escalate” the indent to their manager.
- Whoever approved an indent, for part or full items, must ship.
- All indents are visible to everyone up the hierarchy; so, a higher manager can cut through the layers and directly approve an indent.
Ship and receive: Anyone who approves must ship. Of course, you may not have parts while approving the indent; so, you can ship only when you get the parts. You’ll need to indent for parts to get them.
If you don’t have parts to ship in response to an indent, you can escalate the indent to your manager. You can ship partially or in full. The cycle is completed when the indenter receives the parts.
Spare stock inventory and usage: When the indenter receives the parts, they add them to their inventory, which is their personal stock of spares. Spares are used in repair and maintenance – always related to a ticket. So, regardless of how you received the parts in your stock, you can only use them to solve a ticket.
You have full visibility of the entire spare parts inventory with you and in your direct reporting chain of service users. You also have visibility into the usages and can generate interesting reports regarding spare parts usage for tickets, regions, history of spares used by equipment, and by user. This helps you maintain control over spares used and draw conclusions about equipment maintainability.
Enhancing Maintenance Operations with CMMS Software
Implementing a comprehensive Computerized Maintenance Management System (CMMS) software can significantly improve spare parts inventory management and overall maintenance operations. Such systems can help with:
- Work Order Management: Streamlining the process of creating, assigning, and tracking maintenance tasks.
- Maintenance Planning: Scheduling preventive maintenance and managing corrective maintenance efficiently.
- Inventory Control System: Keeping track of spare parts inventory, including stock levels, reorder points, and usage patterns.
- Stock Optimization: Balancing inventory costs with the need for parts availability to minimize downtime.
- Asset Management: Tracking equipment performance, maintenance history, and lifecycle costs.
- Maintenance Budget: Managing expenses related to spare parts and maintenance activities.
By leveraging these features, organizations can improve their maintenance performance, reduce equipment downtime, and optimize their spare parts inventory management processes.
Leave a Reply