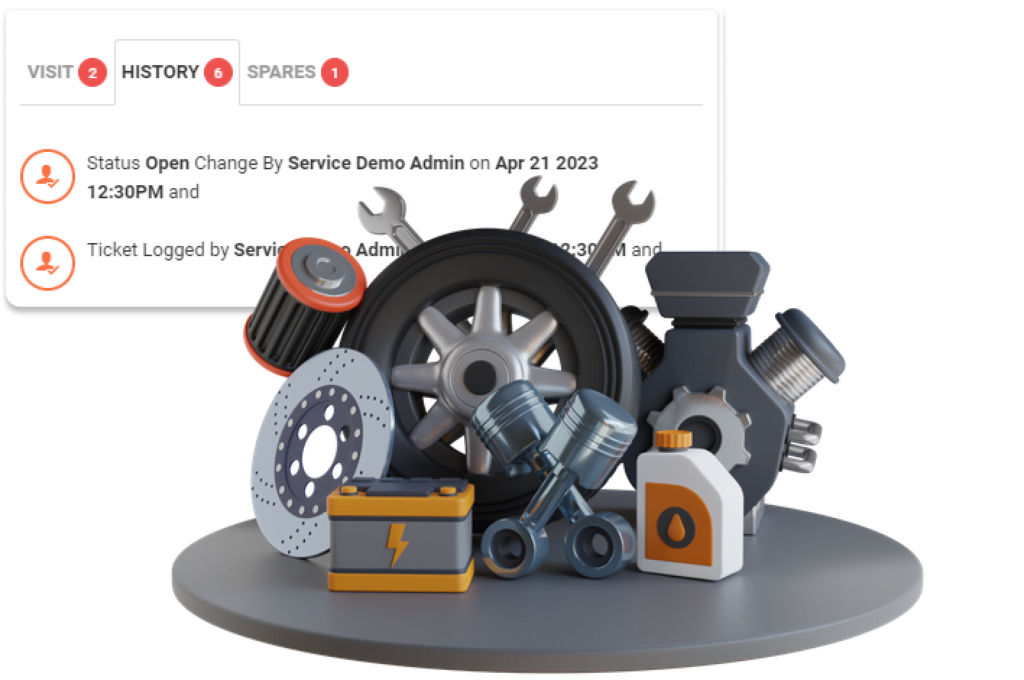
Organize spare parts inventory – track, count and protect
There is a saying that an army marches on its stomach. A well functioning customer service operations needs to organize spare parts in order to be successful.
Spare parts can be the most expensive part of your service delivery. So, it is important to monitor consumption and check for correct usage.
A very simple customer service flow, we posted some time back, was basically about ticket handling- logging tickets (complaints), acknowledging them, assigning it to a field service agent, who would then visit the customer, inspect the equipment, make out an estimate for the repair- items and labour. Once he gets a go-ahead, he starts the repair and once the repair is done, he “closes” the ticket.
Of course, many things were omitted in that diagram. The most glaring omission was the role of spare parts and thus the need to organize spare parts. In this post, we will list and discuss best practices we have observed from our customers who organize spare parts required in their customer service operations.
How does a part “flow” through the system- it reaches the customer (gets fitted into the equipment under repair) from the central warehouse through a linear flow. The following diagram will help you understand how Simply C2 helps to organize spare parts management.
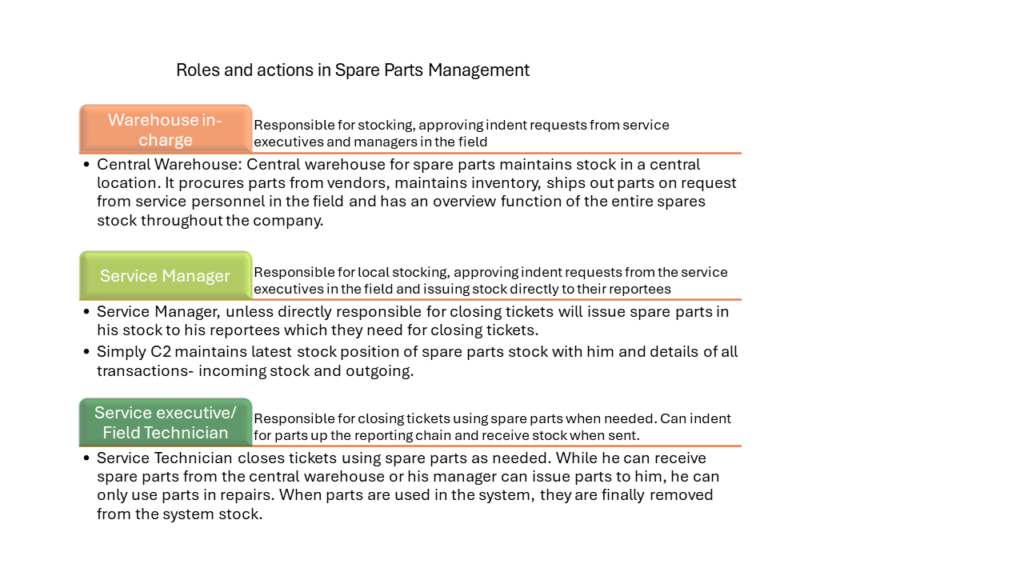
Organize Spare Parts Stocking and Movement
Let’s split this into 3 main parts:
- Maintaining stock in central warehouse
- Maintaining stock in local stock- with regional offices or individuals
- Use of parts in repair (consumption)
While we have covered point 3 above in great detail in the section on repair tickets handling, today we will talk about the aspect of stock keeping – centrally as well locally.
Managing spare stock centrally
1. Keep Track of Every Part
Understanding where each item belongs in your inventory helps you quickly locate the correct parts when needed. Organize spare parts for operational efficiencies. Here are some practical tips to keep your warehouse inventory well-managed:
- Prioritize Common Parts: Store the most frequently used parts at the front for easy access.
- Visibility Matters: Ensure employees can see the inventory both physically and in the database.
- Label Smartly: Use systems like hanging from the ceiling or date labels to know where each part is.
- Stay Ahead on Orders: Maintain a calendar with future purchase orders, due dates, and a list of suppliers with contact details to prevent stockouts.
- Reuse Unused Parts: Don’t discard parts that aren’t immediately needed. Treat your inventory like a resource bank that can come in handy when situations change.
By following these tips, you’ll keep your spare parts inventory organized and easily accessible.
2. In your Central Storage Area: Consolidate and Label
When you get down to organize spare parts, it can be a significant undertaking. So break it down into smaller, manageable tasks.
- Audit Your Current Storage: Evaluate your current storage situation and note how often parts end up stashed and forgotten.
- Find a New Storage Space: Choose a new space for storage, whether it’s a garage, shed, basement, or a room in your repair shop. Measure for shelves and storage containers.
- Collect and Store: Gather all parts and place them on shelves or in bins, making sure to leave room for new items. Keep commonly used parts easily accessible.
- Sort by Function and Manufacturer: Sort items based on their function and manufacturer. Allocate floor space for different categories such as heavy pieces, light items, wires, and fasteners.
- Identify and Troubleshoot: Know what spare parts you have and potential issues with them so you can have the right tools on hand.
- Label Everything: Clearly label all products and containers to avoid searching through boxes. Use a label maker for efficiency.
Warehouse Organization Tip: Implement a bin location system for precise storage of small items. It can be a game-changer for consolidating inventory.
3. Keep Records of Your Parts: Embrace Technology Over Pen and Paper
Maintaining accurate inventory records is essential for having the parts you need when you need them. Manual management is inefficient and time-consuming, so leveraging technology is a smart move.
- Ensure your parts are “mapped” against equipment models- doing this is going to save your people tonnes of time, eliminate mistakes and save money. In Simply C2 our customers can map every spare partno to an equipment model – to ensure the field technician does not end up using the wrong part for repair.
- Implement Spare Part Management Software: Use software to handle routine tasks like receiving, transfers, and write-offs. This helps organize spare parts for technicians and warehouse workers.
- Utilize Inventory Control and Scanning Technology: Ensure you have the right tools for inventory control, scanning, and multi-location management to support business growth.
- Comprehensive Business Management: With systems like Simply C2, you can manage customers, work orders, sales, and inventory all in one place, including warehouse organization.
Investing in the right technology will save you time and resources, making your operation more efficient. By following these steps, you can create a well-organized, central storage area that helps organize spare parts much easier.
Organize Spare Parts stocking locally
If you have a geographically distributed organization, then you have to allow for local stocking of spare parts – at the regional office level, at the individual service technician level or both.
- Track local stock level: Simply C2 shows you at any instant what spare parts are available to which technician and in how many quantities. This makes centralized decision making regarding stocking driven by consumption really simple.
- Indent when you are running low on local stock.
- Always keep sufficient quantity of fast moving stock of spare parts locally.
- Keep expensive spare parts securely in office.
Spare parts management is crucial in ensuring reduced equipment downtime, reduced need for working capital and reduced inventory costs. Sign up for a free account in Simply C2, here and get a head-start, today.
Leave a Reply